Bandung: Advice on technical innovation in the industry
Abstract Member of the Expert Committee of the Coated Abrasives Branch, Professor of the University of Hunan, Wan Long, I came to Tongcheng for the first time. I saw that in such a small, relatively remote county, there are so many coated abrasive companies, and the well-known and largest enterprises in China are here. It feels good. ...
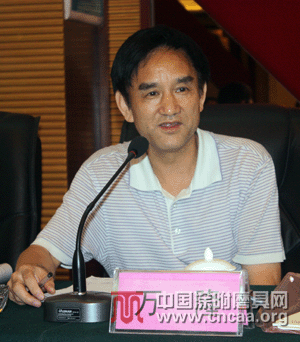
Member of the Expert Committee of the Coated Abrasives Branch, Professor of Hunan University, Wanlong
China's coated abrasives have experienced decades of development. Since the introduction of the first wide belt production line in the 1980s, the belt grinding has been rapidly developed in China. Especially in the past one or two decades, it has developed faster and become an indispensable industry in China's machinery processing industry. The annual output value has reached several billion. In the past two years, China's manufacturing industry has developed to a certain level, and some adjustments must be made. This adjustment will also affect our coated abrasive industry.
At present, the common problems of domestic coated abrasives are that the competition in the industry is becoming more and more fierce. Because relatively speaking, its technical level is not very high, the technical content is not very large, so there are more and more production enterprises, and the market capacity is so large, enterprises must compete with each other; the second is the user's requirements. Higher and higher. The manufacturing industry continues to develop, the precision requirements are getting higher and higher, and the finish requirements are getting higher and higher. Correspondingly, some new requirements will be put forward, especially the requirements for new applications and the requirements for new products. Some new grinding processes have been introduced from abroad, and new product requirements are not suitable for us. In addition, changes in the domestic situation in recent years have also made traditional products face severe challenges. Traditional products are relatively cheaper, competition is more intense, and the pressure to survive is growing. The rising labor costs in the past two years have made the burden of enterprises invisibly aggravated. I don't know what the labor situation is like here. Like Changsha, the wages of employees are at least 2,000, and the coastal areas are more than 3,000 and 4,000. Labor costs have risen very quickly, and the price of products has not been raised, and the cost of raw materials has also risen. The pressure on invisible enterprises is great. This is also a common problem in coated abrasives and other manufacturing companies.
In this situation, how to find a way out. The first few experts have already made a good introduction, I just want to briefly talk about some of my views from a professional point of view. I mainly engage in professionalism. Of course, my profession is not entirely coated with abrasives, but I am in the field of abrasives and abrasives. I have some similar views and exchanges with you.
I think that in the current situation, enterprises must innovate in order to achieve rapid development and stable development. Traditional products and current products have reached a certain scale, and it is necessary to stabilize the quality. And some of the current products, in many cases, are more popular, and there are not many products with real features. Yuli has some special products, but the proportion is also very small. Mainly the main products are mainly road products. So I think that if a company wants to continue to develop, it must have new products. The development of new products should start from the following aspects:
One is innovation in raw materials. The earliest coated abrasives used animal glue, which was gelatin, leather glue and the like, and later developed urea-formaldehyde resin, and then phenolic resin. At this stage of development, I feel that to do high-end, the adhesive should be improved. We have recently studied some polyimide resins for diamond-coated coated abrasives, which are resistant to high temperatures and wear. Not bad. In this regard, we also pay attention to some new materials, such as inorganic polymer adhesives researched by Dr. Xi'an of Xi'an. It is a compound glue, an organic and inorganic compound glue, which was originally a composite rubber for composite materials used in aerospace. It is an organic glue in the inorganic glue, which is compounded. We have done a lot of experiments, using its high-molecular yield performance in the low temperature stage; in the high temperature stage, we mainly use the properties of its inorganic materials. I am still interested in this material, the strength is really strong, the process is relatively simple, and many performances are good, but at present its water resistance is a relatively big problem, can you further improve the performance to be coated? The promotion and application of abrasive tools and fixed abrasives is the key to achieving relatively large breakthroughs.
The second is innovation in the matrix. The base of the coated abrasives was originally made of paper or cloth, and later developed into polymers and glass fibers. At present, coated abrasives like superhard materials develop in the direction of the metal matrix. Diamond coated abrasives like Zhengzhou Reiter, including abrasive belts, page wheels, and some diamond wire saws, all use metal substrates, which is also a direction.
The third is innovation in abrasives. The traditional abrasives are silicon carbide, brown fused alumina, white fused alumina, and later developed into zirconium corundum. Compared with heavy-duty grinding, it is better to use zirconium corundum. The other is the stacked abrasives that everyone is studying. In this process, it is more common to use a resin as a binder to study the stacked abrasives. For example, Yuli Company is a stacked abrasive made by bonding the abrasives together with a resin. At present, we mainly study ceramic bonded abrasives. Because ceramics are relatively brittle, the hardness can be controlled at random. Therefore, after it is made into stacked abrasives, some properties and resin-made stacked abrasives may be different. I think it is more meaningful, and I am currently doing some experiments. In addition to the ceramic abrasive, it is the "SG" abrasive we used to say. The SG abrasive is used in the fixed abrasive tool. After the tool is made, it is applied more. In the application of the abrasive tool, the current application is not too much. I think this may be because the cost of SG abrasives is relatively high, and it is better to achieve a better price/performance ratio. The application of SG abrasives in the application of abrasive abrasives should be achievable. How to match the base and the glue, the higher-grade products, the high-grade abrasives should be matched with high-grade adhesives, which must be matched. . As the saying goes, "Good horses are well equipped with saddles."
The fourth is process innovation. I used to engage in fixed abrasives. In recent years, I have also applied some coated abrasives. There are no obvious boundaries between coated abrasives and bonded abrasives. I also bring some research and development with students now. Many of the products are combined with consolidation and consolidation. At present, several aspects of my research, one is a grinding disc for grinding the glass screen of the mobile phone and the glass screen of the handheld computer. This grinding disc 3M is also produced, mainly by making some resin-bonded diamond particles on the plastic substrate, and sticking it on the film to form a disc, which is a combination of the coated abrasive and the fixed abrasive. Another aspect is the solar photovoltaic material cutting wire saw. China's energy is very tight, so the development of solar energy is an inevitable trend, and the country also pays more attention to it. Its principle is to cut single crystal silicon and polycrystalline silicon into very thin pieces, and then convert the solar energy into electric energy and turn the light into electricity through surface treatment and wiring treatment. Monocrystalline silicon and polycrystalline silicon are first produced into rods with different diameters. The rods are then cut into very thin pieces. Previously, metal wires were used to make silicon carbide powder into slurry, and the wire moved back and forth to add silicon carbide slurry. Going in, the line drives the silicon carbide particles to move for cutting. Nowadays, especially in Japan, they use electroplated wire or diamond abrasive to make a diamond wire saw. This kind of wire saw has higher production efficiency than the original silicon carbide slurry, the width of the processing edge is greatly reduced, and the quality of processing and cutting is also increased. This is a direction in which superhard materials are combined with coated abrasives, and it is estimated to be one or two. There was a relatively large development during the year. The third aspect is to mix the liquid resin and the abrasive into a slurry, then stick it onto the rubber, and then cut into small pieces. This product is currently used in printed circuit boards, which is actually coated with abrasives and A combination of bonded abrasives, these are some of the things I am currently doing.
Coated abrasives can be applied in many fields. Grinding like glass edge, currently using fixed abrasives, especially diamond; and edging of single crystal silicon and polycrystalline silicon wafers, because of the thin thickness, can not be subjected to a large force, while monocrystalline and polycrystalline silicon Very fragile, so this aspect of grinding can be replaced with coated abrasives; there are edging of the screen of the mobile phone, edging of the screen of the handheld computer, and many ceramic processing, etc., many aspects can be used for coating Abrasives, the application of this aspect is still lack of research. According to my opinion, the promotion of some new products should be combined with the application equipment. We have some feelings when we do the fixed abrasives. Although many things are good, it is difficult to promote them. For example, new materials are fixed. This is the case with the promotion in the bearing industry. Abrasives are used in the bearing industry. At present, it mainly uses ordinary abrasives, such as silicon carbide and corundum. Superhard material bonded abrasives have many advantages in this respect, but in the process of promotion, the problem encountered is that the original processing equipment is made of ordinary abrasive tools, and the ordinary abrasive tools can be trimmed with diamonds. If superhard abrasives are used for processing, trimming becomes a problem. They do not have a dressing tool and the installation is problematic. Therefore, the development of the product should be matched with the machine tool. The product and the processing equipment will have a better application. This is some of my experience.
Coated abrasives, including abrasives, are just tools. Relative to mechanical manufacturing, machine tool manufacturing, and the industry is relatively small. In basic research, including product development and process research, the technology is still relatively backward. Therefore, we still have a lot of work to do in this regard. The coated abrasive industry has to be bigger and stronger. The bigger one is mainly relying on economic strength. Many of our enterprises already have scale, but if they are strong, they need comprehensive factors, including economy and management, but more are technical. Go up and be strong. Therefore, the input of the technicians is very important. As a member of the coated abrasives, I hope to make some contributions to the industry. In addition, as an industry association, we must also work hard in the country, especially in terms of new product projects. It is also a very necessary thing to be able to fight for some voice and to support some of our national policies. In this regard, I feel that the superhard side is better than us. As an industry association, this aspect should be strengthened.
China Searun Solar Solution Co., Ltd. , https://www.srsolarlights.com