New progress made in the research of aeroengine combustion technology for the Institute of Engineering Thermophysics
The main development trend of aero engine combustion chambers is the use of high-temperature rising, high-efficiency, and low-pollution combustion technologies. One of the classic structures of active combustion engine main combustion chambers is the TAPS combustion chamber developed by GE, USA, which is used on CFM56 series engines. This type of combustor pre-combustion stage uses a center spray, and the outer ring is equipped with a two-stage swirl swirler (as shown in Figure 1). The liquid mist forms a film by impacting the internal venturi tube, and then undergoes internal and external swirl shearing. After the secondary crushing combustion. However, in the face of the implementation of CAEP8, a new civil aviation air pollutant emission standard, and the strong demand of military aviation for the development of high-temperature rising combustion chambers, existing combustion technologies have already faced challenges.
Recently, the Clean Combustion Research Team of the Light Power Laboratory of the Institute of Engineering Thermophysics, Chinese Academy of Sciences, has developed the LDI combustion technology based on a reversed double swirl venturi premixed (CDV) burner. The CDV burner structure is shown in Fig. 2 shows.
This technology aims to promote efficient, low-pollution combustion of engines while meeting the technical requirements of high-temperature rising combustion chambers. Based on this technology, the researchers developed a variety of lean direct injection combustion chamber structures and obtained invention patents, including a single-tube combustion chamber (shown in Figure 3, ZL201210374686.1), and an annular combustion chamber (as shown in Figure 4, ZL201210375557.4). They rely on the good atomization and combustion performance of CDV burners, and the distributed combustion of fuel and air at the same time, so as to achieve full fuel and air mixing and efficient low-pollution combustion.
The principle of the CDV burner is to generate a strong turbulent shear band by means of an inverted double swirler under the condition of good atomization of the oil nozzle, and to use the venturi contraction section to accelerate the jet toward the center to form a powerful reverse shear aerodynamic force to achieve oil. Auxiliary atomization of droplets and rapid mixing with air. Compared with the existing two-stage cyclone burners, CDV burners have lower fuel and air flow rates for the unit burners due to the fuel and air classification, and the overall structural size becomes smaller; in addition, the size of fuel nozzles becomes smaller and the atomization effect becomes better. There is no need to use the Venturi tube for secondary atomization of oil droplets, so the internal venturi tube is eliminated structurally and the outer sleeve is designed to be in the form of a Venturi tube. This design avoids carbon deposition and coking deformation problems in the venturi internal burner.
At present, the researchers conducted an experimental study on the CDV burner under different conditions to verify its high-efficiency, low-polluting emissions (see Figure 5).
In addition, according to this structure, the researchers discovered and explicitly provided a reversed double-swirler constrained characteristic rule (as shown in FIG. 6) that is different from a mono-swirling flow. On this basis, different constrained ratios were inversely paired. The swirling flow field is divided into three kinds of flow modes: axial growth of the reflux bubble, backflow bubble waist shrinkage, and double reflux bubble.
The research results have been read out at the 18th session of the China Aviation Society's Power Branch Conference on Combustion, Heat and Mass Transfer, and were highly praised by AVIC experts and academies at the aviation industry. paper.
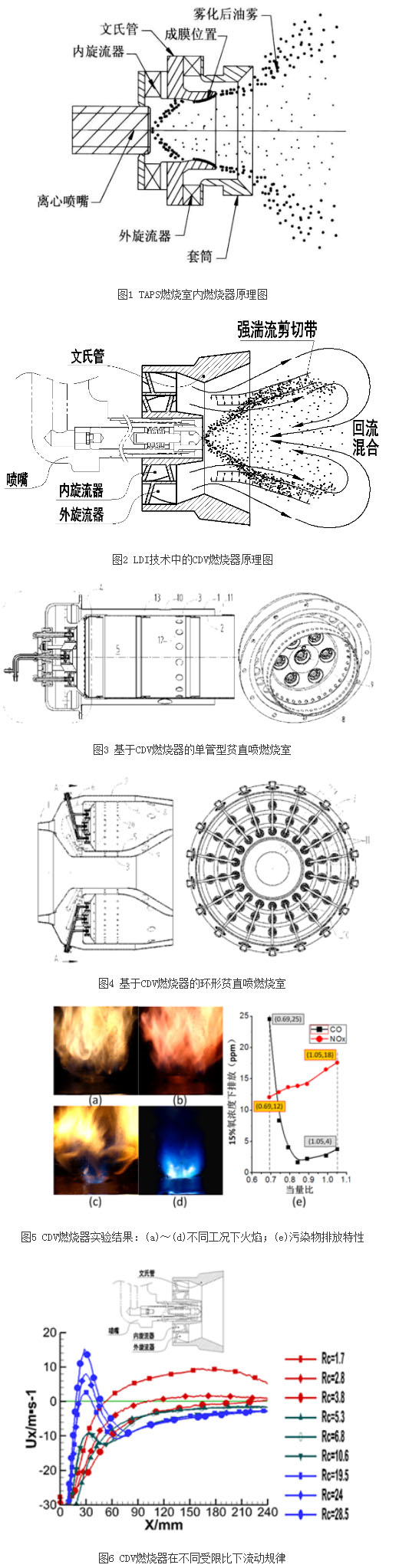
pressure tank is suitable for automatic Polishing Wax spray system, which is highly efficient, energy-saving and convenient!
saving 25% of the polishing liquid, and the high-pressure system can completely penetrate the abrasive on the grinding wheel, which can save 25% of the waste caused by the rotation of the grinding wheel
The tool of automatic polishing wax spray, instead of manual waxing, can effectively improve the polishing efficiency, save labor and raw materials, and strengthen the polishing effect.
pressure tank,spray gun
Jiangmen Gude Polishing Equipment Co., Ltd , https://www.kokipolishing.com