Analysis of the current situation of the use of solid wire for construction machinery
1. The basic situation of the use of solid wire
Our company mainly produces transportation machinery, lifting machinery, earthmoving machinery, road machinery and industrial vehicles. The steel used for the structural parts is mainly low carbon steel Q235, low carbon alloy steel Q345 and structural steel SS400-W. The carbon steel welding wire is mainly ER50-6, ER50-G. The structural parts with higher strength requirements are hot-rolled steel, and the welding wire is made of low alloy steel welding wire ER55-G, ER69-G and ER75-G. The structural parts welding method is mainly CO 2 gas shielded welding and argon-rich welding (CO 2 : O2 = 4:1), and the welding operation is divided into manual welding and robot welding. Manual welding wire specifications are generally φ1.0mm, φ1.2mm. The robot welding wire is generally φ1.2mm and φ1.6mm.
2. Existing problems and solutions
(1) The copper plating has poor bonding force, and the chip is easy to be chipped. Because the surface of the solid wire is copper plated, in the actual welding process, the wire is rubbed with the wire feeding hose and the contact tip, and the copper powder is easy to fall off, thereby causing the wire feeding hose, The contact tip is clogged and damaged. To solve this problem, we can only strictly control the quality of the products and ensure that the copper bonding strength meets the relevant standards.
(2) The copper plating layer is easily absorbed by moisture and rust. If the welding wire is exposed to humid air, there is a problem that the welding wire absorbs moisture and rust, and defects such as pores may occur during the welding process. The wire should be properly stored to avoid moisture. Once the wire spool is opened, it needs to be used up as soon as possible.
(3) Large splash If large welding parameters are selected, the splash is large, the welding operation conditions are poor, and the grinding work is heavy before painting. Therefore, choose reasonable welding current and voltage parameters to reduce splashing. In addition, by brushing the splash-proof liquid around the weld, it is possible to reduce the spatter attached to the workpiece.
(4) Determination of welding parameters of low-alloy high-strength steel welding wire It is necessary to be cautious that the welding process of low carbon steel welding wire is mature, and the welding parameters are determined relatively easily. However, when the welding parameters are determined in the low-alloy high-strength steel welding wire, if the welding parameters are not properly selected, defects such as unmelted roots and pores are likely to occur in the welded joint, see the attached drawings. The existence of these defects reduces the effective bearing area of ​​the welded joint, and the stress concentration of the defective part reduces the tensile strength of the entire joint. During the tensile test of the welded joint, there may be a problem that the weld strength is lower than the strength of the base metal and the sample is broken at the weld.

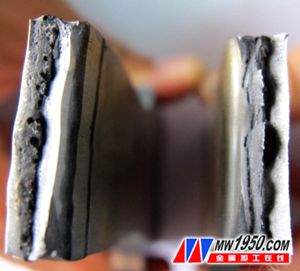
Weld joint defect
3. The future development direction of solid wire
(1) No copper plating wire development The surface of the welding wire is not copper-plated, which can eliminate the problem that the copper powder on the surface of the welding wire falls off and blocks the wire feeding hose and the electric contact nozzle. Copper is a heavy metal that has a great impact on environmental protection and the occupational health of welding personnel. Therefore, the development of non-coppered copper wire, improve the electrical conductivity of the wire, wire feed stability is an urgent need in the welding industry in the future.
(2) The future development trend of high-strength welding wire development engineering machinery is energy saving, environmental protection, and lightweight structural parts. One of the lightweight solutions for structural components is to use high-strength steel instead of ordinary carbon steel, reduce the amount of steel used, and match high-strength steel with high-strength welding wire.
About the author: Ma Rong, Guangxi Liugong Machinery Co., Ltd.
SHOWER TRAY
Shower Tray,sauna and steam bath,Shower Trays,portable steam bath,steam room spa
Guangzhou Aijingsi Sanitary Products Co.,Ltd , https://www.inspirationhottub.com