Thick-walled steel column rolls are difficult to shape and technically
1. There is a problem when thick steel plate is rolled into steel pipe
The Baoji Taiji plant project undertaken by Qinghai Dongda Heavy Equipment Co., Ltd. is a key image project of Baoji City. The main body of the project is a large steel frame structure, which is also the most technically challenging key project undertaken by the steel structure branch. (see picture 1). Among them, the main steel column is made of steel plate rolled into a steel pipe with a diameter of 900 mm and a wall thickness of 25 mm. During the processing, due to the thick wall, the relatively small diameter of the steel pipe, the limited processing capacity of the equipment, the backward welding process, etc., the following problems occurred in the rolling process of the steel plate: 1 The thickness of the coiling machine is limited, and it is impossible to Rolled 50mm thick pre-bend formwork. 2 The circular section of the steel pipe is irregular, and the joint of the steel pipe busbar is severely warped, and the circular section cannot meet the requirements of the regular diameter. 3 The welded joint at the joint of the steel pipe is severely deformed, the surface is not well formed, and the appearance quality is poor. 4 steel pipe rolling efficiency is low.
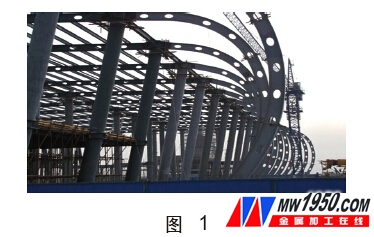
2. Solution
In order to solve the above problems and speed up the construction progress, the steel structure company organized engineering and technical personnel to carry out technical research. Firstly, the two templates are overlapped by plugging to form a composite template, which solves the problem that the coiling machine cannot roll a 50 mm thick pre-bending template. Secondly, the method of using the pre-bending formwork as the tire mold, placing on the bending machine, and pre-bending the steel plate to reach the target diameter in advance, successfully solved the irregularity of the circular section of the steel pipe, and the warpage of the steel pipe bus joint is serious, and the circular cross section cannot be guaranteed. Achieve the problem of regular diameter size requirements. Finally, by adopting a special welding process, the problems of welding deformation at the thick weld seam welded by the traditional welding method, poor formation of the sandwich surface, and poor appearance quality are solved.
(1) Pre-bending formwork (tire mold) is made to ensure that the tire mold is not damaged, and the thickness of the tire mold must be ≥ 2 times the thickness of the steel pipe according to the specifications. Therefore, it is necessary to make a 50 mm thick tire mold to roll a 25 mm thick steel pipe. The existing coiling machine has a maximum coil thickness of ≤34mm. To solve this contradiction, the following method is used to make the tire mold: firstly, two 25mm thick steel plates are respectively rolled into a circular arc with a radius of 475mm and 500mm to form upper and lower molds. Open the hole in the mold. Secondly, the two arc plates are superposed and then subjected to plug welding. Then, the two templates are spot-welded to ensure that the two walls are tight. A lifting nose is left on the tire mold for subsequent use (see Figure 2).
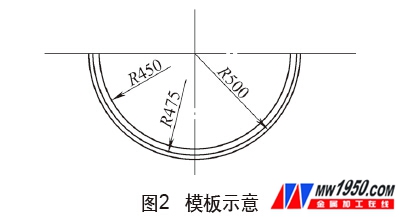
(2) Pre-bending steel plate with tire mold as template to form steel pipe Because the steel plate is directly placed in the roller of the rolling machine, the steel pipe with CNC diameter of 900mm is seriously warped at the joint of the bus bar, and the steel pipe section is irregular. . Therefore, a tire mold having an inner diameter of 900 mm was produced, and the steel sheet was pre-bent. When pre-bending, the tire mold is hung into the roller of the rolling machine, and the steel plate to be rolled is placed. The roller is controlled to move up and down to make the plate and the tire mold close to each other, and then the winding plate is started. The pre-bending distance is 100~150 mm (see Fig. 3). .
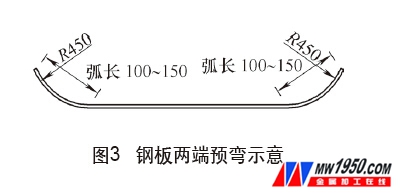
After the steel plate is pre-bent, after removing the tire mold, the numerical control diameter is 900mm target value, and the pre-bending plate is put into the coiling machine to roll out the regular steel pipe. In order to speed up work efficiency, batch roll is performed after batch pre-bending.
(3) The welding process first uses CO 2 gas shielded welding for bottom welding, then submerged arc welding is used for surface welding, and finally the carbon arc gouging is used to clean the welding process from the back root and CO 2 gas shielded welding. The traditional welding method has serious problems such as severe welding deformation at the weld seam after welding, poor formation of the sandwich surface, and poor appearance quality.
3. Innovation superiority analysis
(1) The old and new technology is compared with the original process. The round section of the steel pipe is extremely irregular. The joint of the steel pipe busbar is severely warped, and the circular section cannot meet the requirements of the regular diameter. The weld at the joint of the steel pipe is severely deformed and the surface is formed. Not good, poor appearance quality; steel tube rolling efficiency is low. After adopting the new process, the circular section of the steel pipe is ruled, and the circular irregularity of the steel pipe section is ≤ 2 mm. There is no warpage at the joint of the busbar; the new welding process eliminates the deformation caused by the original welding, so that the quality of the weld meets the requirements of the first-grade weld, the surface of the weld is well formed, and the appearance is beautiful.
(2) The production of the technology innovation point pre-bending formwork and steel plate pre-bending is one of the innovations of this innovation. The innovation solves the problem that the coiler cannot roll a 50mm thick pre-bend formwork. Pre-bending tire molds provide a guarantee for regular coiling of steel pipes. The new welding process is the second innovation of this innovation. If this welding process is not used, the joints of the steel pipe busbars cannot meet the quality requirements of the welding technology. Batch pre-bending and batch rolling are the innovations of this innovation. The batch operation saves time, manpower and material resources for the processing of steel pipes, and greatly improves labor efficiency.
(3) Analysis of the economic benefits generated by the new process After adopting the innovative method, it is not necessary to re-correct the rolled irregular pipe fittings, and the speed of the coiled welded steel pipe is four times. At the same time, it saves a lot of labor costs and materials such as oxygen and acetylene.
About the author: Jin Qi'an, Lu Fulou, Wang Jun, Wang Zhen, Qinghai Huading Industrial Co., Ltd.
ZHEJIANG KINGSIR VALVE CO., LTD. , https://www.kingsir-valves.com