How to use the boiler cleaning agent?
When solid or liquid fuel is burned in the boiler, soot is adhered to both the heating surface of the boiler and the flue. The ash on the heated surface is one millimeter thick, and the thermal conductivity is reduced by about 50 times, which reduces the thermal efficiency of the boiler, increases the energy consumption, shortens the service life, and when the ash accumulation is serious, not only the heat exchange deteriorates but also the resistance increases, which will affect the normal operation of the boiler. It is even forced to stop the furnace to remove soot and affect production. In the past, the removal of soot was done by manual cleaning or steam blowing, which not only labor intensity, cost reduction, and improvement of working conditions, but also benefited the environment.
LX-102 cleaning agent won the 6th China Patent New Product Gold Award, and the Petrochemical and Chemical Industry Department Science and Technology Progress Second Prize in 1994. The A-type oxidation type and B-type catalytic type cleaning agent have been exported to Russia and African countries.
principle:
The alkali metal cation generated by the cleaning agent in the high temperature zone of the furnace adheres to the surface of the boiler tube wall to prevent the deposition of the scale, and the accumulated smog can be completely burned due to the sufficient oxidation of the medicine, and the molten nitrate promotes the smog. The cracks in the hard scale become loose, and the soot is more easily oxidized under the action of the catalyst. During the combustion, the nitrate shock and the generated sulfur generate a gas shock wave under certain action, which causes the scale to fall off more easily, and the nitrate is decomposed. Nitrite also has a certain corrosion inhibition effect on the pipe wall. In addition, the added corrosion inhibitor can slow down the corrosion of the boiler and reduce the formation of sulfur dioxide, so that the fuel is fully oxidized and completely burned. The smoke and carbon monoxide are reduced from entering the atmosphere, and the result of the combustion of the ammonium salt reduces the nitrogen in the flue gas, which is beneficial to environmental protection.
Scope of application:
Can be used for cleaning of various coal-fired oil-fired boilers. The type A drug is oxidized and is more suitable for use in coal-fired boilers with high sulfur content and inferior coal or ash. The appearance is black powder; type B is a catalytic type ashing agent, and the appearance is white granules.
Instructions:
The cleaning agent can be directly placed on the grate by the observation hole. Before the cleaning agent is put into place, the boiler should be in a hot state of burning for a period of time, so that the refractory brick should be in a hot state, and the ashing agent should be burned after the cleaning agent is put into the fire. In severe cases, the chemical gas can be fully contacted with the heated surface of the adhered soot to facilitate the best effect. For the oil-fired boiler, the cleaning agent is first placed in the spray gun dosing tank, and the can lid is covered. Insert the nozzle into the fire hole or the ignition hole (do not insert the nozzle too long, in case the temperature is too high, the chemical agglomeration is not easy to spray), quickly open the compressed air valve, and use compressed air with a pressure of 2-3Kg/cm3. It is sprayed into the furnace in a mist form.
Dosage:
The dosage is five-fifths of the fuel per day, and the initial dose is 2-3 times that of normal. If the scale of the smoke is serious, the duration of the initial administration can be appropriately increased, usually for about one week.
Economic effect:
Using the boiler cleaning agent for 7-16 days, the original accumulated smoke in the boiler can be removed (continuous use can keep the heating surface clean) to improve heat conduction and reduce heat loss. According to the current actual furnace test, the thermal efficiency of the boiler can be increased by 8.1 to 9.6%, the coal saving rate is 18.9%, and the fuel saving rate is 20%.
This product is a new generation product jointly developed by our company and the Institute of High Energy Physics of the Chinese Academy of Sciences. The mechanism is that alkali metal cations generated when burning at high temperature in the furnace are attached to the surface of the boiler tube wall to prevent the scale from being more easily oxidized. Accumulated soot, completely burned, melted nitrate promotes cracks in the hard scale of the scale, and makes the scale easier to oxidize under the action of the catalyst. When burning, the nitrate and sulfur generate gas under certain action. The shock wave causes the soot to fall off more easily. The nitrite produced by the decomposition of nitrate plays a certain corrosion inhibition effect on the pipe wall. In addition, the added corrosion inhibitor can slow down the corrosion of the boiler and reduce the result of sufficient oxidation combustion of the sulfur dioxide-generating fuel. To reduce the infiltration of soot and carbon monoxide into the atmosphere, the result of the combustion of ammonium salts reduces the nitrogen oxides in the flue gas, which is beneficial to environmental protection.
(1) Main components: catalyst, oxidizing agent, decomposing agent, penetrating agent, and the like.
(2) Scope of application: various boilers that use coal as fuel.
(3) Usage: The observation hole is directly placed on the grate. When the cleaning agent is put into the boiler, the boiler should be in a hot state of burning for a period of time. The input of the chemical should be increased, so that the chemical gas and the powder can be made in the case of severe combustion. The attached soot is in full contact on the heated surface for best results.
(4) Dosage: The normal dosage is one-tenth to one-five of the fuel, and the initial dose is 2-3 times of the normal dosage. If the smoke scale is severe, the initial dose can be increased appropriately, and the duration is usually 2-3 weeks.
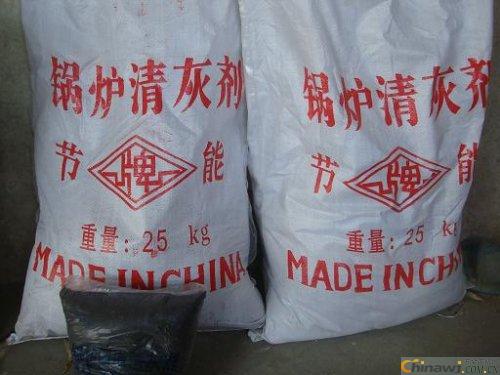
For products reference | ||
No. | Item | Description |
1 | Bearing Bar Size | 25x3, 25x4, 25x4.5, 25x5, 30x3, 30x4, 30x4.5, 30x5, 32x5, 40x5, 50x5, 65x5, 75x6, 75x10---100x10mm etc. |
I bar: 25x5x3, 30x5x3, 32x5x3, 40x5x3 etcUS standard: 1''x3/16'', 1 1/4''x3/16'', 1 1/2''x3/16'', 1''x1/4'', 1 1/4''x1/4'', 1 1/2''x1/4'', 1''x1/8'', 1 1/4''x1/8'', 1 1/2''x1/8'' etc. | ||
2 | Bearing Bar Pitch | 12.5, 15, 20, 23.85, 25, 30, 30.16, 31, 32.5, 34.3, 35, 38.1, 40, 41.25, 60, 80mm etc. |
US standard: 19-w-4, 15-w-4, 11-w-4, 19-w-2, 15-w-2 etc. | ||
3 | Cross Bar Size and Pitch | Twisted bars 5x5, 6x6, 8x8mm; Round bars Dia.6, 7, 8, 9, 10, 12mm and so on. |
38.1, 40, 50, 60, 76, 80, 100, 101.6, 120, 135mm, 2'' & 4'' etc. | ||
4 | Material Grade | ASTM A36, A1011, A569, Q235, S275JR, SS400, Mild steel & Low carbon steel, etc. |
Stainless steel SS304, SS316.s335jr | ||
5 | Surface Treatment | Black, self colour, hot dip galvanized, painted, powder coating, electrolytic polishing. |
6 | Grating Style | Plain / Smooth, Serrated /teeth, I bar, serrated I bar. |
7 | Standard | China: YB/T 4001.1-2007, USA: ANSI/NAAMM(MBG531-88),UK: BS4592-1987, Australia: AS1657-1985,Germany: DIN24537-1-2006, Japan: JIS. |
8 | Panel Size: | 3x20ft,3x24ft,3x30ft,5800x1000, 6000x1000, 6096x1000,6400x1000, as request |
9 | Application: | oil refinery,petroleum and chemical Industry, Seaport and airport, power plant, transportation, papermaking, medicine, steel and iron, food, municipality, real estate, manufacturing,metallurgy,railway,boiler,etc |
Steel Grating,Steel Bar Grating,Galvanized Steel Bar Grating,Steel Bar Grating For Bridge
HEBEI KAYI BUILDING MATERIAL TECHNOLOGY CO.,LTD , https://www.kayimesh.com