Application of new induction technology and new technology in automobile manufacturing
First, the principle and characteristics of induction heating
Electromagnetic induction
Electromagnetic induction refers to a conductor placed in a varying magnetic flux that produces an electromotive force. This electromotive force is called an induced electromotive force or an induced electromotive force. If this conductor is closed in a loop, the electromotive force will drive electrons to flow and form an induced current (see Figure 1).
The discovery of electromagnetic induction is one of the greatest achievements in the field of electromagnetism. It not only reveals the internal connection between electricity and magnetism, but also lays an experimental foundation for the mutual transformation between electricity and magnetism, which opens the way for humans to obtain huge and cheap electric energy, which is of great significance in practical use. The discovery of electromagnetic induction marks the arrival of a major industrial and technological revolution. It has been proven that electromagnetic induction is the basis for the operation of generators, induction motors, transformers and most other electrical equipment. It is widely used in electrical, electronic, electrification, automation and industrial heating to promote the development of social productivity and science and technology. It has played an important role.
2. Induction heating principle
The application of induction heating technology is the working principle of the transformer. After the alternating current is applied to the inductor (the primary coil of the transformer), an alternating magnetic field is generated around it, and the metal workpiece placed near it (short-circuit secondary of the transformer) The coil) generates an electromotive force under the action of an alternating magnetic field, and under the driving of the electromotive force, the electrons flowing in the workpiece form an induced current (the eddy current is shown in Fig. 2). The electrical energy is converted into thermal energy by the resistance of the workpiece to heat the workpiece itself.
3. Advantages of induction heating
As described above, induction heating directly achieves heating of the workpiece by using an induced current generated in the metal. The heating method is a non-contact heating, and the electrothermal conversion efficiency mainly depends on the magnetic permeability of the metal material and the coupling degree of the inductor (the primary coil of the transformer) and the workpiece (the secondary coil of the transformer), that is, the magnetic of the metal The higher the conductivity, the higher the thermal conversion efficiency, the tighter the coupling between the inductor and the workpiece, and the higher the thermal conversion efficiency. In ordinary furnace heating, a heating source is needed, and the metal workpiece is heated by the radiation of the heating source, the convection of the heat in the heating medium, and the heat conduction of the heated body. The heating efficiency is the energy conversion of the heating source. The efficiency, the convection efficiency of heat, and the overall efficiency of the conduction efficiency of heat in the heated body. In contrast, induction heating has the following advantages:
(1) There is no heating process for convection and conduction, which is directly heated inside the workpiece and the heating speed is fast.
(2) Reduced oxidation and decarburization of the workpiece during heating.
(3) Energy saving, no need for preheating and heating of the heating furnace required for heating in the furnace, heating can be started and stopped at any time, and it is not necessary to maintain the temperature of the heating furnace during non-working periods.
(4) The heating time is short, the production efficiency is high, and the process cost is effectively reduced.
(5) Local heating of the parts can be achieved.
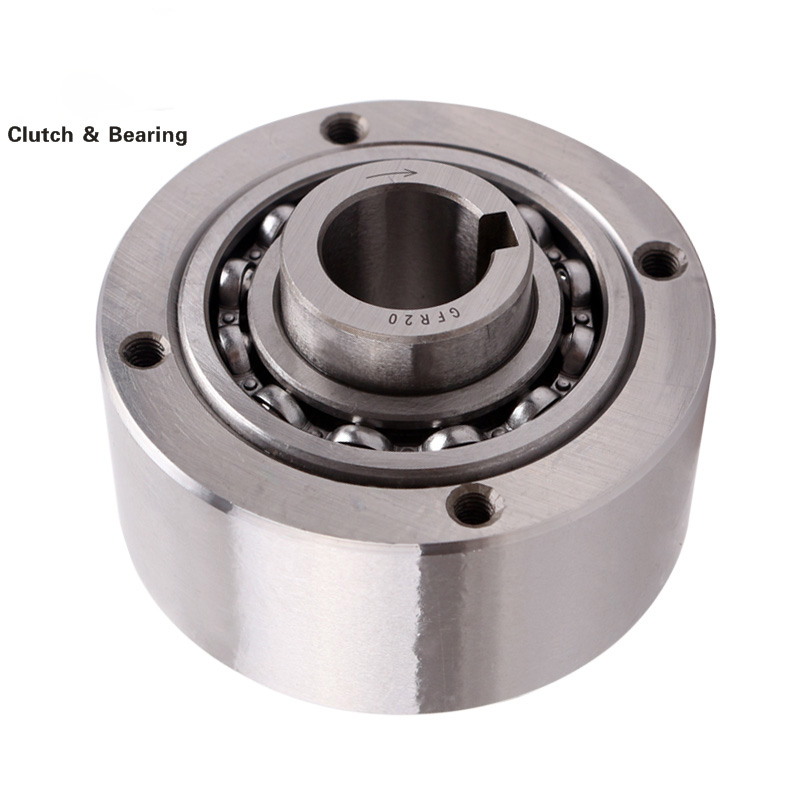
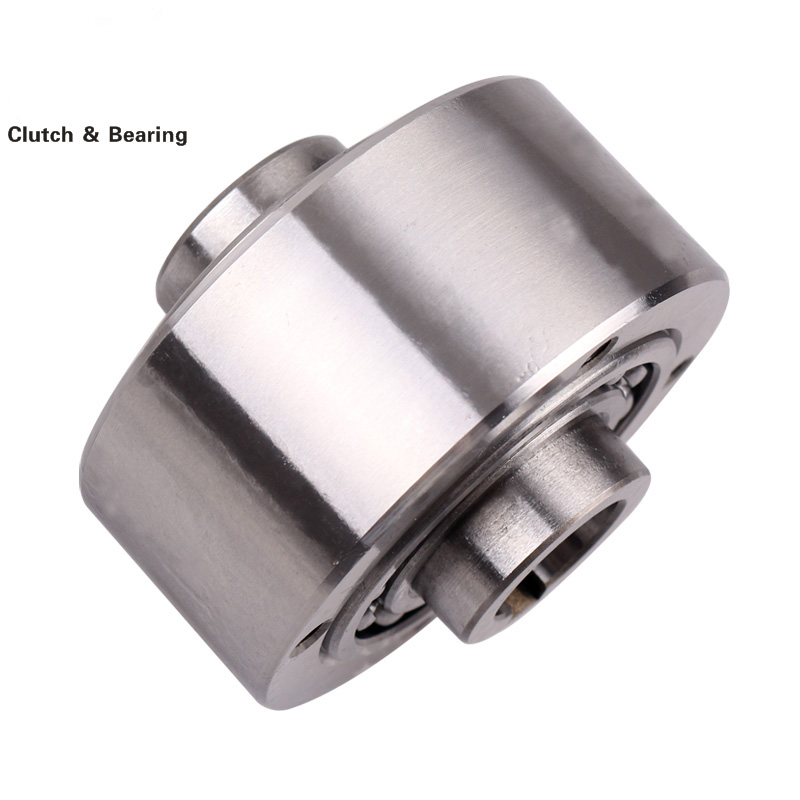
Electromagnetic induction
Electromagnetic induction refers to a conductor placed in a varying magnetic flux that produces an electromotive force. This electromotive force is called an induced electromotive force or an induced electromotive force. If this conductor is closed in a loop, the electromotive force will drive electrons to flow and form an induced current (see Figure 1).
The discovery of electromagnetic induction is one of the greatest achievements in the field of electromagnetism. It not only reveals the internal connection between electricity and magnetism, but also lays an experimental foundation for the mutual transformation between electricity and magnetism, which opens the way for humans to obtain huge and cheap electric energy, which is of great significance in practical use. The discovery of electromagnetic induction marks the arrival of a major industrial and technological revolution. It has been proven that electromagnetic induction is the basis for the operation of generators, induction motors, transformers and most other electrical equipment. It is widely used in electrical, electronic, electrification, automation and industrial heating to promote the development of social productivity and science and technology. It has played an important role.
2. Induction heating principle
The application of induction heating technology is the working principle of the transformer. After the alternating current is applied to the inductor (the primary coil of the transformer), an alternating magnetic field is generated around it, and the metal workpiece placed near it (short-circuit secondary of the transformer) The coil) generates an electromotive force under the action of an alternating magnetic field, and under the driving of the electromotive force, the electrons flowing in the workpiece form an induced current (the eddy current is shown in Fig. 2). The electrical energy is converted into thermal energy by the resistance of the workpiece to heat the workpiece itself.
3. Advantages of induction heating
As described above, induction heating directly achieves heating of the workpiece by using an induced current generated in the metal. The heating method is a non-contact heating, and the electrothermal conversion efficiency mainly depends on the magnetic permeability of the metal material and the coupling degree of the inductor (the primary coil of the transformer) and the workpiece (the secondary coil of the transformer), that is, the magnetic of the metal The higher the conductivity, the higher the thermal conversion efficiency, the tighter the coupling between the inductor and the workpiece, and the higher the thermal conversion efficiency. In ordinary furnace heating, a heating source is needed, and the metal workpiece is heated by the radiation of the heating source, the convection of the heat in the heating medium, and the heat conduction of the heated body. The heating efficiency is the energy conversion of the heating source. The efficiency, the convection efficiency of heat, and the overall efficiency of the conduction efficiency of heat in the heated body. In contrast, induction heating has the following advantages:
(1) There is no heating process for convection and conduction, which is directly heated inside the workpiece and the heating speed is fast.
(2) Reduced oxidation and decarburization of the workpiece during heating.
(3) Energy saving, no need for preheating and heating of the heating furnace required for heating in the furnace, heating can be started and stopped at any time, and it is not necessary to maintain the temperature of the heating furnace during non-working periods.
(4) The heating time is short, the production efficiency is high, and the process cost is effectively reduced.
(5) Local heating of the parts can be achieved.
1 | 2 | 3 | 4 | Next page |
CLUTCH RELEASE BEARING
A clutch release bearing unit engages and disengages the clutch, via the diaphragm spring and pressure plate. It includes
provisions to guide the fork or piston radially.
Our compact design combines a precision sheet metal bearing unit and polymer sleeve or carrier, for manual gearbox applications against a dry clutch. We offer multiple designs with inner or outer ring rotation for a variety of applications.
The units are designed to account for many constraints, including: automated manual transmission or dual clutch transmission. higher operating temperature; and increased application loads.
provisions to guide the fork or piston radially.
Our compact design combines a precision sheet metal bearing unit and polymer sleeve or carrier, for manual gearbox applications against a dry clutch. We offer multiple designs with inner or outer ring rotation for a variety of applications.
The units are designed to account for many constraints, including: automated manual transmission or dual clutch transmission. higher operating temperature; and increased application loads.
Specification
MODEL
|
70x116.6x27mm Japan Original Auto Clutch Release Bearing CT70B
|
MOQ
|
1PCS
|
Guarantee
|
50,000km or 1 year
|
Type
|
Brand new Type
|
Price
|
Factory Price
|
Brand
|
SEMRI
|
Aftermarket
|
Oem Replacement
|
Size
|
Same as original
|
Package
|
1.one pcs one box
2.White box and carton 3.Customer brand design |
Reference Items of clutch release bearing :
NO.
|
NSK NO.
|
KOYO NO.
|
NTN NO.
|
NACHI NO.
|
VKC3581
|
24TK308E1U3
|
RCT356SA8
|
FCR48-11/2E
|
55SCRN41P-6
|
VKC3584
|
35TMK29C1
|
RCT356SA9
|
FCR47-8-4/2E
|
55TMK09-1
|
VKC3588
|
50TKB3504BR
|
RCTS33SA1
|
FCR44-9/2E
|
55TMK804
|
VKC3592
|
50TKB3501BR
|
RCTS33SA3
|
FCR44-36-1/2E
|
55TRK30W1
|
VKC3598
|
50TKA3805
|
RCT363SA
|
FCR44-25-4/2E
|
60SCRN033
|
VKC3600
|
33TKD03U3
|
RCT371SA
|
CT52A-1
|
60SCRN31P
|
VKC3602
|
50TKA3305R
|
RCT37SA1
|
63TNK001
|
60SCRN31P-6
|
VKC3606
|
48TKB3204R
|
RCT38SLI
|
60TMK20
|
70TNK-1
|
VKC3607
|
48TKB3202
|
RCT40
|
55TRK30A/2E
|
BC11S3
|
VKC3609
|
48TKA3301
|
RCT401SA
|
55TMK804
|
|
VKC3610
|
48TKA3214
|
RCT4064SL1
|
55TK30A
|
|
VKC3615
|
48TKA3211B
|
RCT4067A2RS
|
40TMK29
|
|
VKC3675
|
48TKA3210
|
RCTS355SA
|
40TMK20
|
|
VKC3616
|
48TKA3201
|
RCT4075-1S
|
|
|
VKC3666
|
35TMK29B2
|
RCT40SA3
|
|
|
VKC3668
|
47TKB3102B
|
RCT422SA1
|
|
|
VKC3617
|
47TKB3101
|
RCT45-1S
|
|
|
VKC3618
|
47TKB3001A
|
RCT473SA
|
|
|
VKC3621
|
47TKB2901UN3S
|
RCT55B
|
|
|
VKC3622
|
45TKD07U3
|
RCTS28SA
|
|
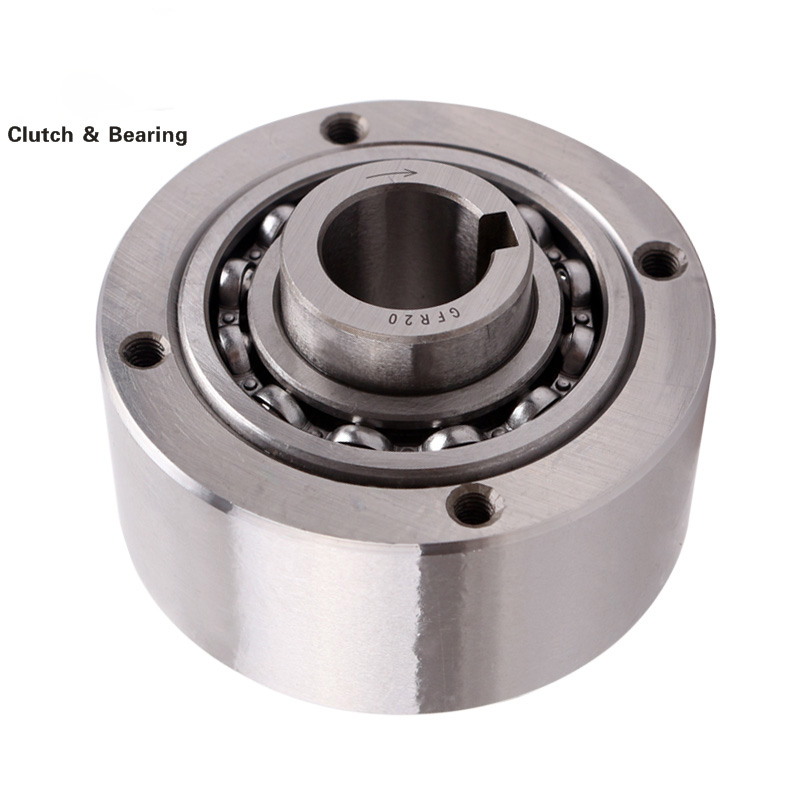
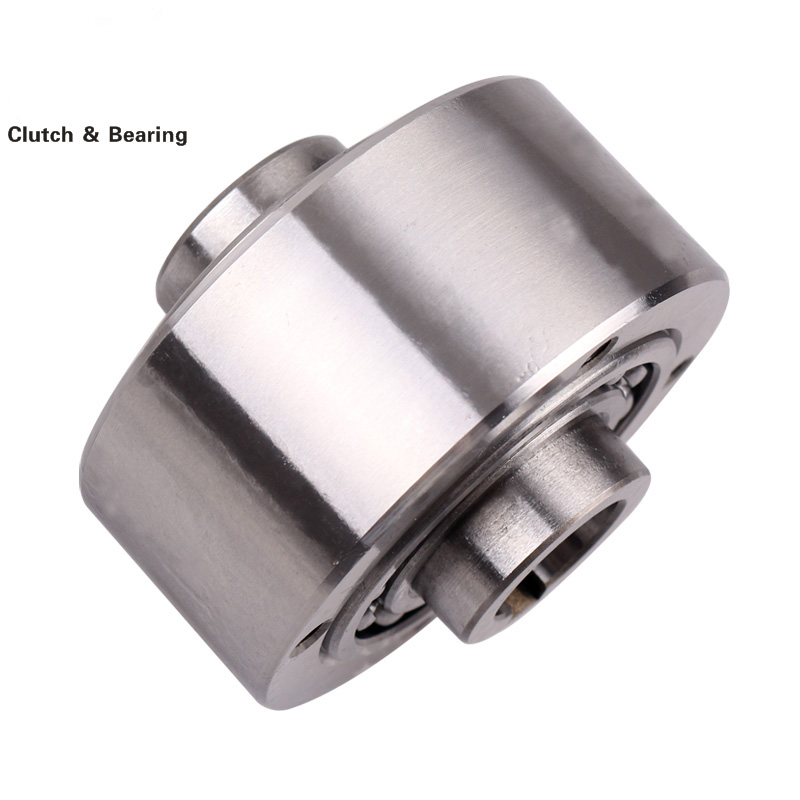
Clutch Bearing,Auto Clutch Release Bearing,Clutch Release Bearing,Clutch Bearing For Auto
Shijiazhuang Longshu Mechanical & Electrical Equipment Trading Co., Ltd. , https://www.longsbearings.com