Welding process of Inconel625 alloy
Nanjing Chemical Industry Co., Ltd. 90,000 tons/year hydrogen production and supporting air separation project, designed by Sinopec Nanjing Engineering Co., Ltd., is located in the nitrogen fertilizer zone of Nanhua Company, Liuhe District, Nanjing, and is pressurized by GE Coal Water Slurry. The entrained-flow coal gasification technology and large-scale industrial equipment use high-sulfur coal as raw material to produce hydrogen, which not only conforms to the overall development strategy of Jiangbei Chemical Belt, but also conforms to the national policy of coal chemical industry.
The project has long pipelines and many kinds of pipeline materials, including low carbon steel, alloy steel, stainless steel and Other materials. The pipeline features are complex and there are many welding methods. Both manual welding and automatic welding are used, and the welding materials are more complicated. Among them, the oxygen pipeline adopts a special material, Inconel625 alloy, which is a kind of metal material which is based on iron, nickel and cobalt and can work for a long time under the high temperature of 600 ° C and certain stress; High temperature strength, good oxidation and corrosion resistance, good fatigue properties, fracture toughness and other comprehensive properties. In order to prevent the mechanical properties of the Inconel625 alloy steel pipe from being damaged after welding, a more targeted welding process must be used in the welding process. The welding process of Inconel625 alloy steel pipe will be described below in conjunction with the project site construction conditions.
First, the physical properties and chemical composition of Inconel625 alloy:
1. Physical characteristics:
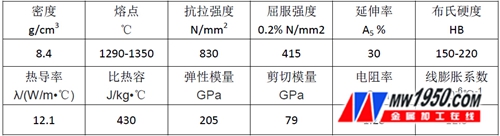
2. Chemical composition:

Second, the metallographic structure of Inconel625 alloy:
Inconel 625 has a single-phase structure and is a face-centered cubic lattice structure. When it is kept at about 650 ° C for a long time, carbon particles and unstable quaternary phases will be precipitated and converted into stable Ni 3 (Nb, Ti). Square lattice phase. The molybdenum and niobium components in the nickel-chromium matrix after solid solution strengthening will improve the mechanical properties of the material, but the plasticity will be reduced.
Third, the weldability of Inconel625 alloy:
1. In the Inconel625 alloy, the high content of Cr and Mo provides the alloy with better resistance to pitting corrosion and fission corrosion, and it still has corrosion resistance even under high temperature conditions;
2. Inconel625 alloy, Cr content of up to 22.2%, improve the strength of the alloy, a certain amount of Mo also makes the alloy's creep strength improved, while a small amount of Al and Ti, the alloy's age hardening effect is reduced to a lower To the extent that the weldability of the alloy is improved;
3. In the Inconel 625 alloy, due to the presence of a certain amount of S and P, the segregation coefficients of S and P are the largest among various elements, and at the same time, S and P can form various low-melting compounds or eutectic in steel, and Because Ni is an element that strongly stabilizes the γ phase, lowering the solubility of S, increasing the possibility of formation of low-melting eutectic, and facilitating the formation of hot cracks;
4.Inconel625 alloy has a large linear expansion coefficient, but the thermal conductivity is small, resulting in uneven heating and cooling of the alloy, so that the plastic strain of the alloy occurs in the high temperature stage. The plastic strain is larger, the more easily cracked. ;
5.Inconel625 alloy is a nickel-based alloy, the solid-liquid phase temperature spacing is small, the solidification speed is fast, and it is easy for the oxygen or water vapor in the liquid molten pool to overflow and form pores;
Fourth, the welding process of Inconel625 alloy:
According to the physical properties and weldability of Inconel625 alloy, in order to retain the corrosion resistance and other excellent properties of Inconel625 alloy, and depending on the wall thickness, tungsten argon arc welding (GTAW) or argon welding (GTAW+SMAW) is selected. The welding method and the following targeted measures for its weldability:
1. Preparation before welding:
a) Take measures against wind and moisture, use windshield for outdoor construction, reasonably plan construction, minimize welding on site, and do not apply welding to environmental requirements that do not meet specifications and design requirements;
b) The groove angle is processed to 65°, the large groove is favorable for gas overflow in the molten pool, and the weld forming factor is greater than 1, and for arc welding, the weld metal crystallization is weakened at the center line of the weld In the case of intersection, the possibility of cracks, pores and inclusions is reduced;
c) Chemical cleaning of pipes, welding consumables, welding tools, etc., to remove surface oxides or other low-melting compounds, and to ensure that the welds and the sides of the groove are clean and dry within 20 mm, avoiding the addition of impurities in the molten pool. Produce slag or other defects;
d) The inside of the pipeline is filled with argon gas to reduce the oxygen, water, phosphorus, sulfur, nitrogen, etc. in the air to dissolve into the molten pool;
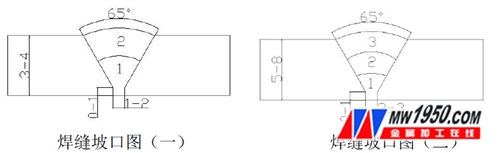
2. Precautions during welding:
a) Control the welding heat input. For the small weld and the base metal due to overheating or excessive heating time, the grain is coarse. Multi-layer welding is used. The thickness of each layer is not more than 4~5mm, and the small current is selected. Welding, beading and beading are staggered by 10mm welding, and each welding is separated by a certain time, after the interval temperature drops to 60 °C ~ 150 °C, and then continue welding;
b) When welding the initial weld bead, the welding wire is slowly fed from the middle of the weld to observe the root of the groove. When a circular melt hole appears on both sides of the groove, it indicates that the root has been penetrated. When the welding encounters the welding metal The welding metal must be polished and then welded;
c) The welding slag and debris between the weld bead and the weld bead must be cleaned before continuing to weld. If the weld cannot be completely welded due to delay, and the weld is re-welded, the weld must be re-welded according to the process requirements. After the surface is treated, the welding is continued;
d) Use the scratching method to start the arc in the groove, and do not lead the arc outside the groove to avoid the contamination of the base metal and the cracks and pores caused by the welding; use short arc welding to reduce the splash and pores, and cover with the crescent Surface welding, evenly oscillate the electrode to about 1mm from the groove surface, and use the reflow arcing method or rounding arc method to close the arc to avoid the occurrence of pores and cracks in the arc pit. When the argon arc welding receives the arc, the arc pit is cooled. Then remove the protective gas;
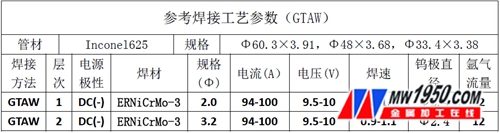
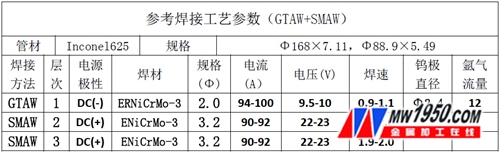
3. Precautions after welding:
a) After welding, the surface of the weld is tested, and the weld height is controlled below 1~1.5mm. The excessively high residual height will cause the internal stress of the weld to concentrate on the weld toe, making the weld toe prone to cracks. When it is too high, use a sander to reduce the residual height;
b) small welding current and uniform welding method can reduce the undercut defect, but when the weld seam has undercut, it needs to be repaired and polished to a smooth transition according to the depth of the undercut;
c) Pay attention to the protection of the weld after the welding is completed, to avoid the rapid cooling and pollution of the weld by rain or other substances when it is not completely cooled to normal temperature;
d) After the pipeline hydraulic pressure test is finished, the pipeline is chemically cleaned again to make the weld metal have good corrosion resistance;
5. Welding equipment of Inconel625 alloy:
Because of the welding method of argon welding, in order to reduce the labor intensity of the staff, choose an inverter welding machine (model: ZX7-315S/ST) that meets both argon arc and hand arc welding, argon arc welding (GTAW) Select DC positive connection, and electrode arc welding (SMAW) select DC reverse connection.
The inverter welding machine has excellent IGBT inverter technology, and the power source used by the welding machine has stable steep drop (or constant current) external characteristics, and has various argon arc operation modes, high frequency arc ignition, and strong welding penetration force. With electrode arc welding function, stable performance, strong anti-interference ability, saving energy;
6. Welding materials of Inconel625 alloy:
Due to the choice of welding method of tungsten argon arc welding (GTAW) or argon electric welding (GTAW+SMAW), considering various factors, the welding wire is selected: ERNiCrMo-3, the welding rod is: ENiCrMo-3, these two welding materials For welding, the basis is as follows:
The chemical composition of ENiCrMo-3 is as follows

The chemical composition of ERNiCrMo-3 is as follows:

1. Chemical composition of welding consumables: ERNiCrMo-3 welding wire and ENiCrMo-3 welding rod have similar composition to the base metal according to the chemical composition of the welding consumable, and the content of Mn or Si is higher than that of the parent material. The material is slightly larger, these two elements play a positive role in the deoxidation or desulfurization of the molten pool metal, contributing to less porosity and cracking tendency. Elements such as Ni, Cr, Co, Mo also act on the alloying elements in the molten pool metal. To supplement, reduce the adverse effects caused by dilution of base metal alloy elements;
2. Mechanical properties of welding consumables: The strength grades of ENiCrMo-3 welding rods and ERNiCrMo-3 welding rods are in the same grade as the parent metal, the tensile strength is greater than 760 MPa, and because the base metal has thermal crack sensitivity, it is necessary to select crack resistance. Good low-hydrogen welding rods, ENiCrMo-3 welding rods and ERNiCrMo-3 welding wire meet the requirements;
3. The environment and performance of the weldment: Inconel625 alloy steel pipe transports oxygen, in a corrosive working environment, need to choose corrosion-resistant welding consumables, ENiCrMo-3 welding rod and ERNiCrMo-3 welding wire are nickel-based welding consumables, in composition The Cr element content is large, and the Cr element can be supplemented for the deposited metal, so that the corrosion resistance of the Inconel 625 alloy is continued in the weld metal;
4. The domestic nickel-based welding consumables process and performance are lacking compared with some foreign brands. In order to ensure the weld quality and appropriate cost, the imported ENiCrMo-3 welding rod and ERNiCrMo-3 welding wire are selected, and the quality of the welding consumables can be good. Reducing rework in welding operations and reducing construction costs to a certain extent;
Seven, summary
1. Tungsten argon arc welding (GTAW) or argon electric welding (GTAW+SMAW) is an efficient and high quality welding method for welding such nickel-based alloys such as Inconel 625 alloy;
2. Welding Inconel625 alloy, must fully understand its weldability, and according to its use characteristics, develop a reasonable and targeted welding process for welding;
3. A good welding process must be carefully carried out in the welding operation to ensure the welding quality of the weld;
As an excellent alloy material, Inconel625 alloy has great advantages in corrosion resistance and high temperature properties. It is gradually being widely used in the petrochemical industry. The welding technology of this alloy is also becoming mature. The progress has been added.
kaiping aida sanitary ware technology co.,ltd , https://www.kpfaucets.com